Your Trustful Drive Supplier
Servo drive is usally referred to as an amplifier, takes the command signal for position, speed or torque requirement and adjusts the voltage or current applied to the servo motor using closed loop control. Industrial servo drive is a very important component which determines the performance of servo system. Automation drive has the advantages of smaller footprints, tighter tolerance, higher levels of precision. According to these precision capacilities, CNC servo drives and controls are used in robotics, CNC machining, automation, and even in the processes of manufacturing semiconductors.
Showing all 11 results
-
Allen-Bradley
22A-A4P5N104 New Allen-Bradley AB PowerFlex 4- 0.75 kW (1 HP) AC Drive
Read moreRated 0 out of 5 -
Allen-Bradley
22B-A2P3N114 New Allen-Bradley AB PowerFlex 40- 0.4 kW (0.5 HP) AC Drive
Read moreRated 0 out of 5 -
Allen-Bradley
22C-D6P0N103 New Allen-Bradley AB PowerFlex 400- 2.2 kW (3 HP) AC Drive
Read moreRated 0 out of 5 -
Allen-Bradley
25A-A1P6N104 New Allen-Bradley AB Rockwell PowerFlex 523 0.2kW (0.25Hp) AC Drive
Read moreRated 0 out of 5 -
Allen-Bradley
25A-A2P5N104 New Allen-Bradley AB PowerFlex 523 0.4kW (0.5Hp) AC Drive
Read moreRated 0 out of 5 -
Allen-Bradley
25A-A4P8N104 New Allen-Bradley AB PowerFlex 523 0.75kW (1Hp) AC Drive
Read moreRated 0 out of 5 -
Allen-Bradley
25B-A2P5N104 New Allen-Bradley PowerFlex 525 0.4kW (0.5Hp) AC Drive
Read moreRated 0 out of 5 -
Allen-Bradley
25B-A4P8N104 New Allen-Bradley PowerFlex 525 0.75kW (1Hp) AC Drive
Read moreRated 0 out of 5 -
Allen-Bradley
25B-A8P0N104 New Allen-Bradley AB PowerFlex 525 1.5kW (2Hp) AC Drive
Read moreRated 0 out of 5 -
Allen-Bradley
25C-A2P5N114 New Allen-Bradley AB PowerFlex 527 0.4kW 0.5Hp AC Drive
Read moreRated 0 out of 5
REQUEST A QUOTE FOR MORE DETAILS
All You Need to Know About Drive
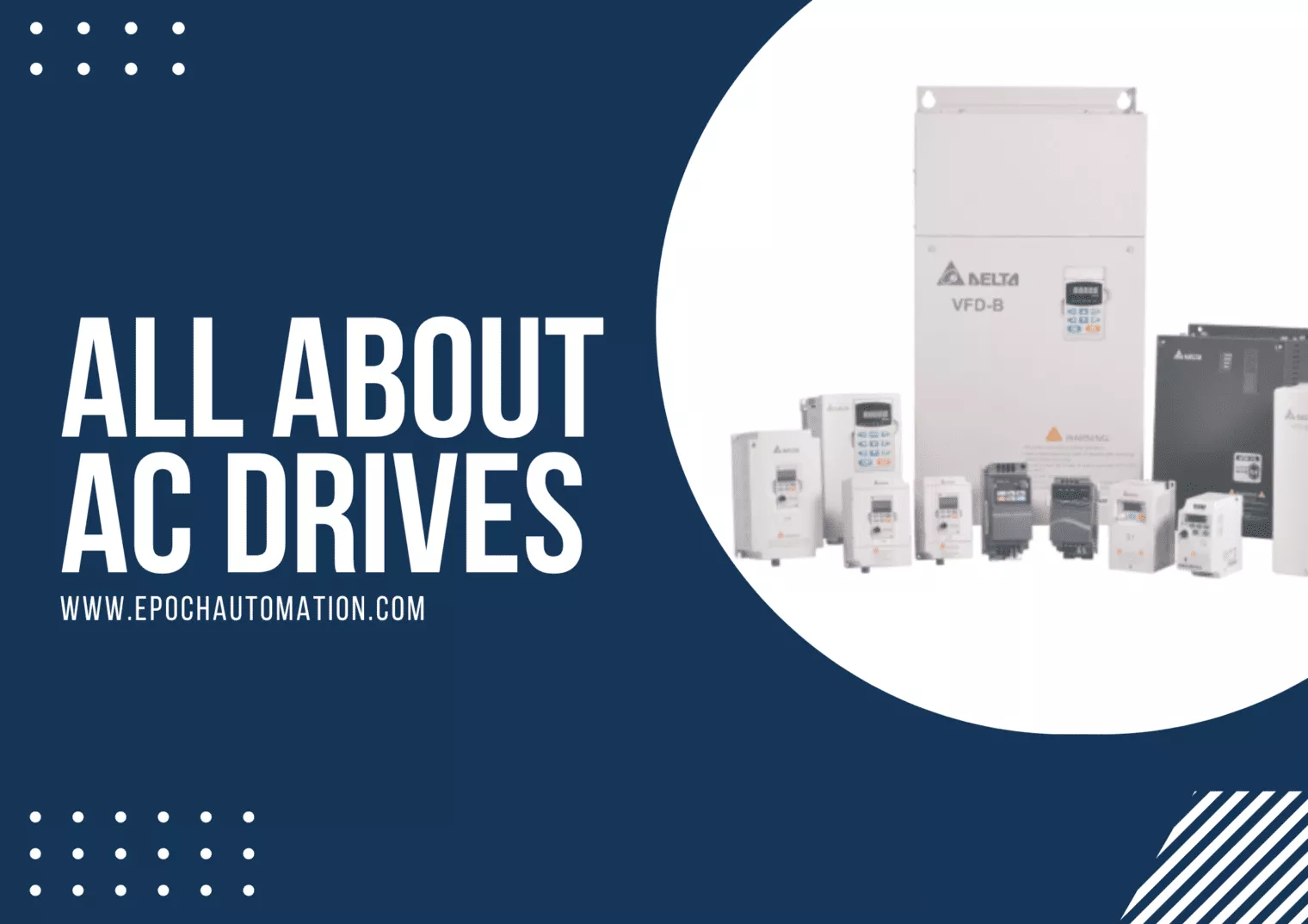
Features of Frequency Converter
An industrial AC drive, also known as a variable frequency drive (VFD), features the ability to control the speed of an electric motor by adjusting the frequency of the power supply, offering key capabilities like precise speed regulation, energy savings through load-based speed control, soft start/stop functionality, overload protection, and various monitoring and diagnostic features, making it ideal for a wide range of industrial applications.
Variable Speed Control
Primary function is to precisely control motor speed by adjusting the output frequency, allowing for fine-tuned operation based on application demands.
Energy Efficiency
Reduces energy consumption by only delivering power needed at a given load, especially beneficial in applications with fluctuating loads like pumps and fans.
Soft Start and Stop
Provides gradual acceleration and deceleration of the motor, minimizing mechanical stress and extending equipment lifespan.
Torque Control
Ability to regulate torque output, important for applications requiring consistent force like conveyors or elevators.
Protection Features
Includes overload, overcurrent, overheat, undervoltage, and overvoltage protection to safeguard the motor and drive from damage.
Closed-Loop Control
Utilizes feedback sensors to monitor motor speed and adjust output accordingly, ensuring precise control and responsiveness.
User Interface
Provides easy access to parameters and settings through a display panel or communication protocols like Modbus or Ethernet.
Self-Diagnostics
Built-in diagnostics to identify potential faults and facilitate troubleshooting.
Multi-Function Programming
Capability to configure various operating modes and control strategies based on application needs.
Power Factor Correction
Can improve power factor by optimizing motor current draw, reducing utility costs.

How Does the AC Drive Work?
An AC drive, also called a Variable Frequency Drive (VFD), works by converting incoming AC power to DC power using a rectifier, storing it in a DC bus, and then using an inverter to convert that DC back into AC power at a variable frequency, which allows precise control over the speed and torque of an electric motor connected to it; essentially, by adjusting the frequency of the AC output, the motor speed can be controlled.
What Are Applications of AC Drive?
AC drives, also known as Variable Frequency Drives (VFDs), are commonly used in applications like HVAC systems to control fan and pump speeds, conveyor systems to regulate belt speed, machine tools to manage spindle speeds, pumps and compressors for optimized motor control, industrial automation for precise motor control across various machinery, and renewable energy systems to regulate generator output, all aiming to reduce energy consumption and enhance operational efficiency; essentially, any application where precise speed control of an electric motor is needed.
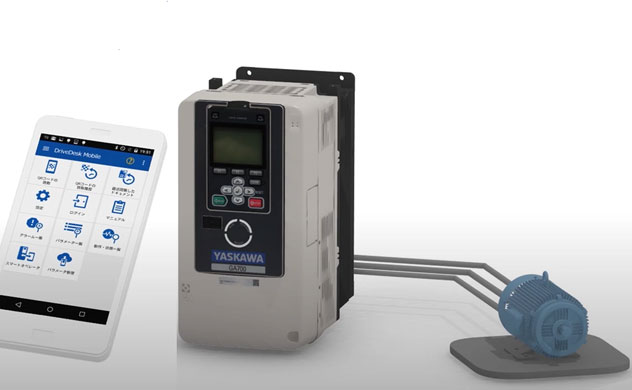
AC Drives (Variable Frequency Drives)
Most common type, allows precise speed control by adjusting the frequency of the power supplied to the motor.
DC Drives
Used for applications requiring high torque at low speeds, often with a closed-loop control system.
Servo Drives
Provide high precision and fast response, ideal for applications like robotics and CNC machines.
Soft Starters
Used to limit inrush current during motor start-up, reducing stress on the power grid.
Microdrives
Compact and economical AC drives for basic variable speed applications.
Belt Drives
Suitable for applications requiring smooth power transmission and flexibility in shaft alignment.
Chain Drives
Used for high power transmission and applications where precise positioning is needed.
Synchronous Motors
Maintain consistent speed even under load changes, useful for applications requiring precise speed control.
Things to Consider:Choose Industrial Drives
When choosing an industrial drive, key considerations include: motor type compatibility, required torque, voltage and phase, operating environment, speed control needs, efficiency, duty cycle, application-specific requirements, and potential for future expansion; ensuring the drive is suitable for the specific motor and application while providing the necessary power and control features for optimal performance in the given environment.
#1 Motor type
Different motors (AC induction, permanent magnet synchronous, DC) have different compatibility with various drives; ensure the drive is designed for the motor you’re using.
#2 Torque requirements
Evaluate the necessary torque to move the load in your application, as this directly impacts drive selection.
#3 Speed control needs
Consider whether you need precise speed control, variable speed operation, or just basic on/off functionality.
#4 Voltage and phase
Match the drive voltage and phase to your power supply and motor.
#5 Operating environment
Choose a drive rated for the temperature, humidity, dust, and other environmental conditions where it will be used.
#6 Efficiency
Select a drive with high efficiency to minimize energy consumption, especially for continuous operations.
#7 Duty cycle
Consider the percentage of time the motor will be running at full load to ensure the drive can handle the required duty cycle.
#8 Application-specific features
Depending on the application, you might need additional features like regenerative braking, overload protection, or communication protocols.
#9 Future expansion potential
Think about whether the drive can be easily scaled or upgraded to accommodate future needs.
Request A Free Quote
We'd like to work with you
Send us a message if you have any questions or request a quote. Our experts will give you a reply within 24 hours and help you select the right valve you want.
- +86 175 0301 5773
- +86 189 2656 9286
- info@yingwangxin.com